Innovation, Efficiency, and Reliability in Power Conversion
We design our product not as a single entity, but as an integral and valuable element of our client’s system and targeted application. We create complex high-performing solutions in the simplest way possible, guided by a philosophy based on a design-for-manufacturing approach. We are continuously innovating to support the trends toward products with reduced size, higher power and maximal reliabil-ity.
Our R&D center located in Paris is comprised of experts in power electronics who consider all mechani-cal and thermal factors and develop fine-grained, real-time, embedded software to deliver the best performing power converters.
Given the importance of time-to market and development cost, we have streamlined the client’s proto-type validation process by providing a custom Simulink testing platform for all our converters, built on digital twin technology. These model-based testing assets are used in the development of our clients’ systems, enabling engineers to refine their designs with utmost certainty.
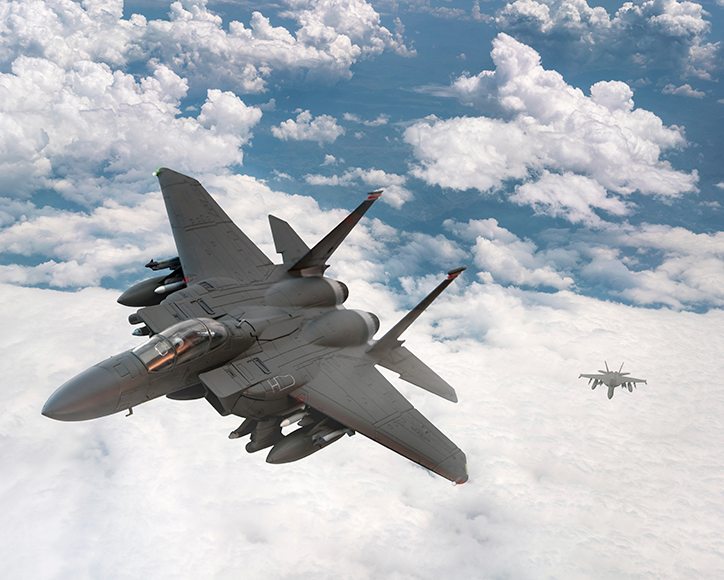
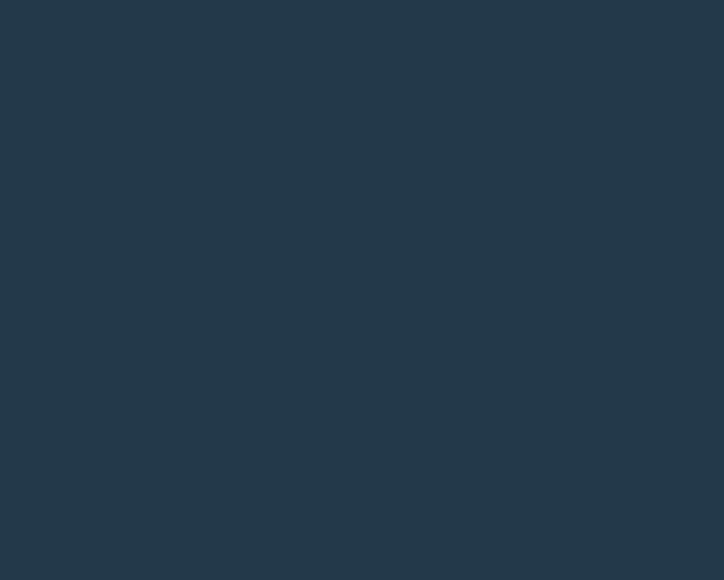
Prototyping and Serial Manufacturing of Converters and Inverters
BrightLoop designs power converters and inverters with a focus on industrial, economic, and reliability constraints, using design-for-manufacturing techniques. Prototypes are developed and tested at our Paris R&D center with industrialization in mind. Low- to mid-volume series, up to 5,000 converters annually, are managed at our Lannion facility, where we handle all product assembly and testing. Our flexible, modular manufacturing process supports global scalability, and facilitates partnerships with EMS (Electronic Manufacturing Services) providers for high-volume production. This strategy ensures we can efficiently meet growing global demand while maintaining high standards of quality and reliability.
Overseeing system design, assembly, and testing enables faster iterations, cost savings, and a more synchronized approach to innovation and production. This integrated concept allows us to control the entire process from conception to manufacturing, ensuring quality assurance and effective supply chain management.
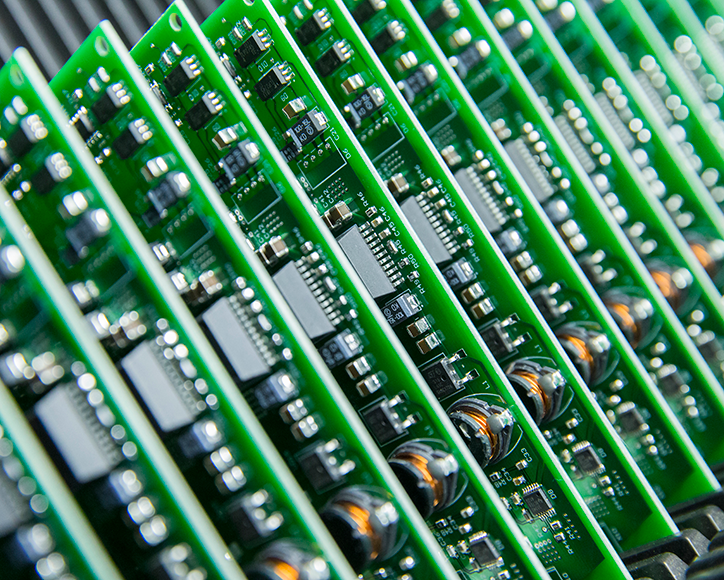
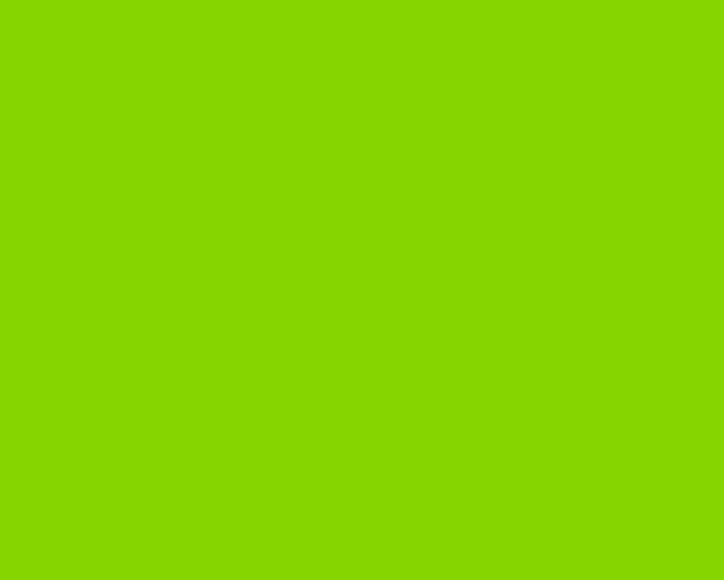